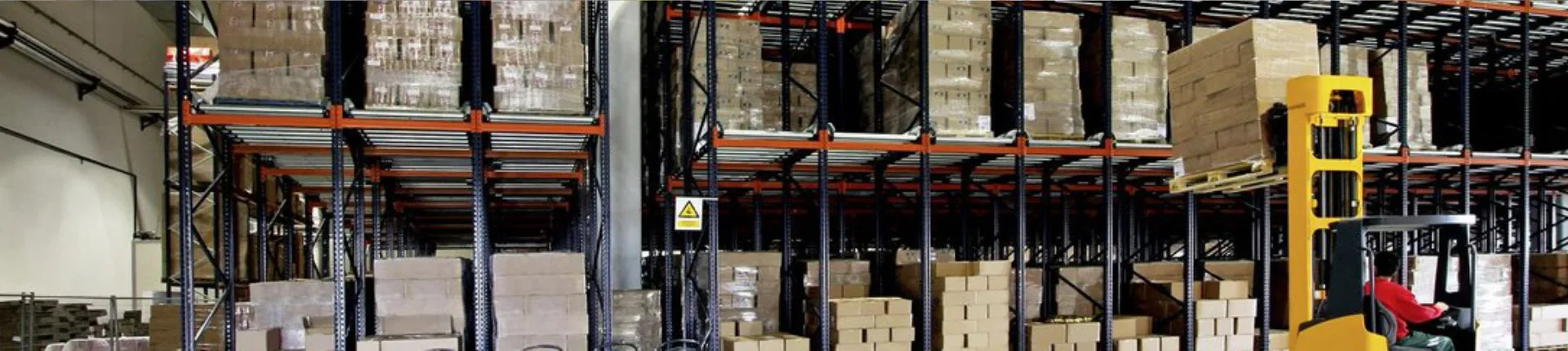
At Potten & Pannen, pencil and paper have been eliminated by the WMS system for maximum efficiency
About the customer
A proudly Czech company that has been bringing a culture of quality, healthy and imaginative cooking to homes and businesses for more than 27 years. Potten & Pannen - Staněk is an unrivalled leading importer, distributor and retailer of premium kitchenware for B2C and B2B customers. In addition to its e-shop and wholesale, today it operates 11 own stores in the Czech Republic and Slovakia. Potten & Pannen - Staněk is an exclusive importer, distributor and retailer of the world's most prestigious brands such as Zwilling, Emile Henry, KitchenAid, Mauviel, Rosenthal, Villeroy & Boch and Polar. The company has almost 100 employees and a headquarters and warehouse in Čestlice.
THE SITUATION BEFORE THE INTRODUCTION OF THE COMPREHENSIVE SOLUTION
The warehouse goods receipt process was performed using pre-printed receipts, which caused higher labour intensity during goods receipt and a possible risk of errors when transcribing data both in the shop floor and during the subsequent transcription of data into the ERP. The possibility of obtaining information on the storage of goods in the warehouse directly from the system was missing.
- Headquarters and warehouse in Čestlice near Prague
- Vision 32 information system
- Warehouse area of 2000m2 - pallet warehouse with overstock, lower location for picking, three-storey gallery for small and smaller assortment
- The warehouse was managed using paper and pencil (so called paper warehouse) - problems with tracking goods, difficult and inefficient work with paper and consequently errors in transcribing data into the information system, lack of control of picked goods, inefficient work with the use of warehouse capacities
- The warehouse is divided into a receiving area and a dispatch area - lack of space
PROJECT OBJECTIVES
- Improvement of warehouse processes - reduction of errors
- Increase in the number of warehouse requests processed
- Flexible access to all necessary information across departments and associated cost reduction and increased productivity
- Flexible warehouse response to non-standard situations
- Minimisation of the proportion of unrecorded work
- Speeding up warehouse processes, especially picking
SOLUTION
- Implementation of a managed warehouse system - K.Motion Warehouse Edge (formerly HighJump Warehouse Edge)
- Connection of an additional module for picking control - K.inspector and its connection to the customer's ERP and WMS
- Supply of Zebra MC33N0-G mobile terminals with Android operating system and Zebra DS2278 barcode scanners
- Supply of Extreme Networks AP7522 Wi-Fi network
- Supply of Zebra ZT230 desktop label printers
- Complete durable labeling of warehouse locations in accordance with analytics - increasing visibility of warehouse and storage areas
RESULT
- The WMS managed warehouse system covered all key processes from pre-arrival, receiving, stacking, picking, packing, checking through to despatch.
- Inspection of picked goods using the K.inspector add-on module - checking all items, automatic invoicing, printing delivery notes, carrier labels.
- In all these processes, the warehouse handler works with a Zebra MC33 mobile terminal equipped with a barcode scanner, which is connected online to the warehouse management system
- Very fast deployment of the managed warehouse system (3 months)
RESULT THROUGH THE EYES OF THE CUSTOMER
"By deploying a managed warehouse system, we gained an overview of the location and flow of goods in the warehouse. The system guides our staff sequentially through the warehouse locations, which has increased the speed of picking and other warehouse operations. We can now control and coordinate all activities in the warehouse, leading to greater efficiency, productivity and avoiding errors. Online we can monitor the processing of individual warehouse operations and stock levels. We can recommend cooperation with KODYS to everyone."
Pavel Staněk and Miloš Staněk
owners of